Rifling Types 101
How Does Barrel Rifling Work?
In order for rifle and pistol barrels to shoot properly and accurately, the barrel requires rifling. The rifling process is a key part of barrel manufacturing, resulting in lands (bore) and grooves that create a spiral down the length of the barrel. This process is done after there’s a hole in the barrel blank. Rifling can be achieved as either a metal cutting, or cold forming process. The 4 most common types of rifling in modern manufacturing are, in no particular order – button rifling, single point cut rifling, broach rifling, and hammer forging. Although other methods may still be used, these types are typical for the majority of barrels that are on the market, because of their repeatability and manufacturing process efficiency for most barrel applications.
Button Rifling
Button rifling is a cold forming process that swages rifling in the barrel with a carbide tool that has grooves in a specific dimension and twist rate. Button rifling is a single pass operation, where the button is pushed or pulled at a controlled rate through the bore of a barrel blank, resulting in the desired lands and grooves.
Pros of Button Rifling – This cold forming process offers benefits to the finished barrel. It work hardens the surface layer of the barrel, increasing durability and barrel life. It also results in an improved finish, with an Ra significantly lower than either the original bore, or other rifling methods. Because no metal is cut, manufacturers and operators do not have to manage chip control.
Button rifling is also a highly controlled process that is repeatable across an entire production lot. Progressive twist is possible with the button rifling process.
Cons of Button Rifling – With button rifling, an additional stress relieve step is required adding cost and time – the stress relieving operation is used to relieve stress introduced in the bore of the barrel because of the cold forming process. Also, pre-machining of pistol barrel features is not possible, as a uniform outside diameter is necessary due to the swaging performed when button rifling. A unique tool is needed for every twist, as the helix is ground into the carbide button.
Manufacturability – Button rifing is easily done on modern equipment. Servo control of the twist rate, compared to older sinebar or cam technology, has greatly improved the uniformity of twist throughout the barrel, as well as enabled repeatability throughout a production lot. Availability and relatively lower investment of equipment also makes button rifling an advantageous method.
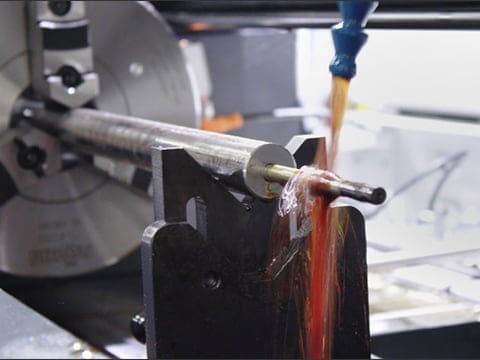
Manufacturing Cost – Tooling – low / Machine – low / Cycle time – low
Popularity – Because of the simplicity, consistency, and short cycle time that button rifling offers, this is by far the most commonly used process in rifle barrel manufacturing by volume.
Typical Applications – Hunting rifles, MSR style rifles as well as some precision rifles and some pistols.
Video Reference – View the button rifling process.
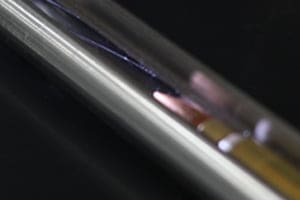
Single Point Cut Rifling
Also referred to as Hook Rifling, this is a metal cutting process that uses a carbide “hook” to cut a single groove in the barrel. The process requires several passes to cut the groove to its final depth. The tool cuts one of the grooves, indexes, then cuts the next groove and indexes again until the desired number of grooves have been cut. The hook is advanced out or deeper via a wedge type system, and the process is repeated. The whole cycle may include many passes to achieve the final depth of the groove in a barrel.
Pros of Cut Rifling – The metal cutting process does not introduce additional stresses in the metal, as compared to a cold forming processes, so the barrel does not require post stress relieving. Manufacturers have great control over groove depth due to the minimal depth of cut per pass and the number of passes per cycle. By simply running another pass, the groove can be cut slightly deeper to achieve the desired groove diameter.
Because the tools are not specific to a twist rate, manufacturers are able to use a single tool for a range of rifling configurations. Advancements in modern machine design and servo technology allow operators to easily program a gain twist with the same tool, while modern CNC technology enables a simpler, more repeatable operation.
Cons of Cut Rifling – Cut rifling is a very time consuming process due to the number of cuts and minimal amount of material removed per cut. It does require a skilled tradesman to operate the machine and process parameters as compared to other rifling methods, where variables are highly controlled by the machine. Repeatability is hardest to maintain with cut rifling. Bore diameter uniformity before the cut rifling process is very important as the cut rifling tool body locates on the bore while cutting the groove.
Manufacturability – A purpose built machine with custom tooling is required and is often custom built by the barrel manufacturer. With cut rifling, repeatability and stiffness of the rotation relative to linear motion is critical and difficult to achieve both in machine design and manufacturing process.
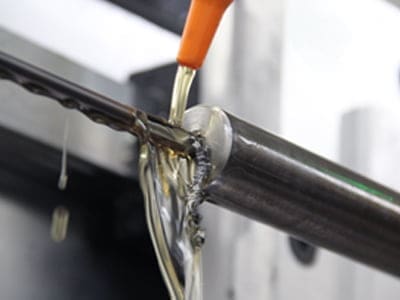
Manufacturing Cost – Tooling – medium; Machine – medium; Cycle time – high
Popularity – Cut rifling is still a common manufacturing process, but cut rifled barrels only make up a small percentage of barrels on the market.
Typical Applications – High end precision rifles
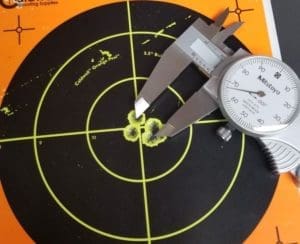
Broach Rifling
Broach rifling is a metal cutting process that uses a long tool with multiple teeth that take small amounts of material out of each groove. The broach is fed down the barrel with a rotation that matches the twist ground in the tool, with each progressive tooth increasing the depth of cut. This is a similar process to single point cut rifling, but only requires a single pass. It can be done on a similar machine to that of button rifling.
Pros of Broach Rifling – Simiar to cut rifling, additional stress is not introduced into the material. However, broach rifling does offer a distinct cycle-time advantage, which is more comparable to that offered by button rifling, by using a single pass.
Cons of Broach Rifling – With broach rifling, a tool is needed for every twist rate, and the tool design prohibits progressive twist. Chip control is an important consideration for manufacturers. Finally, surface finish is not as smooth as that resulting from other rifling processes. Tooling costs can be very high, and the tools are relatively fragile, potentially adding even more costs or interrupting production.
Manufacturability – A dedicated machine and tooling inventory are necessary for the broach rifling process. Tooling design is intricate, which can drive investment. Broach rifling for pistol barrels uses upstream manufacturing, allowing manufacturers to machine outside features, and then broach rifle, eliminating multiple setups.
Manufacturing Cost – Tooling – high; Machine – low; Cycle time – low
Popularity – Because of the upstream manufacturing efficiencies, broach rifling is a popular process for pistol barrels.
Typical Applications – Pistol barrels, some rifle barrels
Hammer Forging
The cold hammer forging process pushes an oversized metal tube over a hardened mandrel, which has the negative of the grooves ground into the outside profile. With some modern mandrels, the chamber is also included. During the process, the tube is fed and forged in small sections, and results in a finished barrel blank that is formed not just to the desired twist and caliber, but also length and sometimes, outside contour.
Pros of Hammer Forging – A metal forging process results in increased barrel durability. Hammer forging also reduces the number of finishing steps, shortening cycle time and lowering manufacturing costs. The hammer forging process, once setup and proven, is very repeatable for production barrel manufacturers.
Cons of Hammer Forging – Hammer forging requires a high initial investment for dedicated machinery. Similar to other rifling methods, a specific mandrel is required for every twist, and progressive twist is not possible.
Manufacturability – This method requires dedicated equipment and tooling which is specific to the process, but can offer advantages due to reduced overall processing steps and total time from raw material to finished product. Machine and tooling advancements, such as the ability to chamber during the forging process, have made hammer forging more justifiable.
Manufacturing Cost – Tooling – high; Machine – high; Cycle time – low
Popularity – Due to high initial investment, hammer forging is less popular than other rifling processes. When it is used, it is typically for rifle barrels at high production levels.
Typical Applications – Military rifles and MSR platform civilian rifles
We use a button rifling process with our 100, 200, 300, and 400 Series barrels. Our 500 Series barrels are single point cut rifled.
With the appropriate machine tools and automation, there’s no limit to how many barrels can be produced in a short period of time! One of Vortakt’s fully automated rifling cells is capable of producing 3,600 barrel blanks each week.
Vortakt recently retooled one of its rifling cells to accommodate large volume production of heavy .50 caliber barrel blanks. The Gorbel crane system is able to accommodate workpieces in excess of 100 lbs with lengths of up to 45”, raw material with an outside diameter of 3.0”, and bore diameters as large as 20mm.
Many factors tie into the cost of rifling a barrel. Material costs, order quantity, tooling cost, cycle time, and countless other variables come into play. For an exact cost breakout of barrel blank pricing, simply submit a request for quote and we’ll get some estimates sent your way!